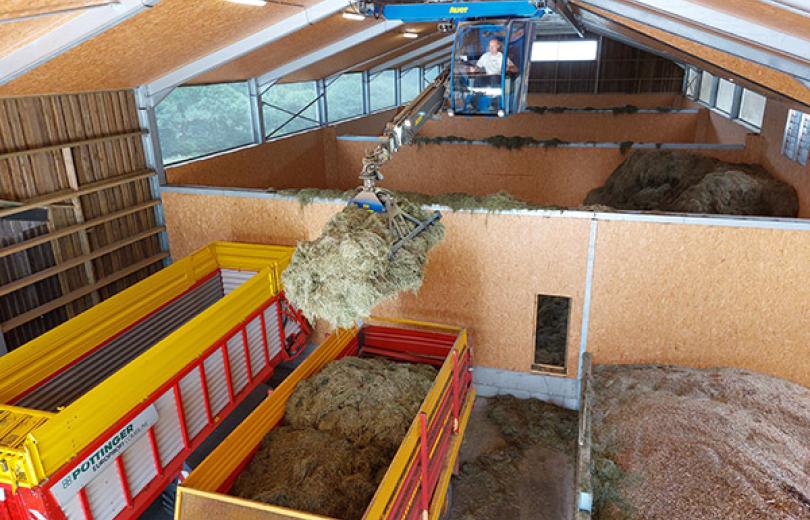
Sécher du foin en grange est une technique permettant de produire et conserver un foin de haute qualité. Si la solution classique lors de l’installation d’un séchoir fait appel à un déshumidificateur, l’utilisation d’une chaleur issue de biomasse est également une option d’intérêt.
C’est par exemple déjà le cas pour valoriser la chaleur excédentaire d’une unité de biométhanisation. Jusqu’à récemment, aucun séchoir à foin en Wallonie n’était équipé d’une chaudière biomasse spécifiquement dédiée à cet usage. C’est maintenant chose faite avec l’installation de la ferme de Monsieur Philippe Counasse à Stoumont. Retour sur ce projet aujourd’hui pleinement opérationnel.
Un projet mûrement réfléchi
En 2015, au cours d’une journée dédiée au séchage en grange, Philippe Counasse a pour idée de s’équiper d’un séchoir à foin en vrac. Les avantages pour cet éleveur laitier, qui fournit en lait la fromagerie de son frère sur le même site, sont multiples. Le séchoir :
- permet d’avoir un foin de haute qualité à disposition toute l’année ;
- ne présente pas de risque de mauvaise fermentation comme avec l’ensilage ;
- conserve tout l’arôme du foin pour un lait de qualité et une valeur nutritionnelle du foin plus élevée en permettant de faucher à un stade plus précoce, ce qui se traduit par une économie sur les achats de compléments alimentaires du bétail.
Alors que ses silos-tours d’ensilage vieillissaient, M. Counasse se questionnait de plus en plus sur la méthode à choisir au moment du renouvellement des équipements. La question énergétique a rapidement été au centre des préoccupations, en comparaison avec la consommation alors nécessaire pour remplir et vider les silos-tours ou utiliser la mélangeuse avec les balles enrubannées. Lors de son travail de fin d’étude consacré au séchage en grange par déshumidificateur électrique, son fils Damien arrive à la conclusion que cette solution ne serait pas rentable dans leur cas: investissement dans les bâtiments dédiés et dans le déshumidificateur électrique de l’air, cabine et puissance électrique conséquente nécessaires, forte augmentation de la consommation électrique, etc.. De plus, la volonté de Philippe Counasse était d’utiliser au maximum les énergies renouvelables et de pouvoir piloter son installation selon la meilleure utilisation du mix énergétique renouvelable disponible à un instant donné.
Une chaudière biomasse pour sécher le foin, et pourquoi pas ?
Lors de la Foire de Libramont en 2018, un premier contact avec ValBiom l'amène à investiguer la piste d’une production d’air chaud au moyen d’une chaudière biomasse. En effet, l’association d’éleveurs français SEGRAFO, accompagnant les projets de séchage de fourrages, avait conclu que de l’air réchauffé pouvait être utilisé au même titre que de l’air déshumidifié. L’exploitation laitière produisait et valorisait déjà des plaquettes bocagères comme sous-couche de litière, pourquoi ne pas valoriser les 16 km de haies pour produire également son propre combustible ? Après avoir visité l’installation d’un producteur de plaquettes équipé d’un générateur direct d’air chaud alimenté en combustibles bois, cette piste est écartée faute de trouver une solution technique satisfaisante (absence de gestions automatiques d’allumage/extinction et de puissance). Seule une chaudière biomasse semblait en mesure d’apporter les garanties de fiabilité nécessaires pour la production de chaleur pour le séchoir.
S’ensuit alors la recherche d’un prestataire capable de dimensionner et mettre en œuvre une solution de séchage au départ d’une chaudière biomasse. C’est finalement la firme française Séchage Concept qui est retenue, laquelle se penchait aussi pour la première fois sur l’utilisation d’une chaudière biomasse avec ce projet. Fort de ses nombreuses réflexions sur les meilleures combinaisons à mettre en œuvre, Philippe Counasse a également décidé de nombreux choix techniques pour son séchoir.
Une combinaison judicieuse d'équipements
Le résultat est un nouveau bâtiment accueillant trois cellules d’une capacité de 100 t de matière sèche chacune (15 x 10 m, sur 7 m de hauteur), une zone supplémentaire de séchage à plat (appelée aussi plateforme multi-produits) utilisable pour sécher des céréales ou des plaquettes de bois, et enfin une zone pouvant accueillir deux bennes et leur tracteurs. Le chargement et déchargement des séchoirs est assuré au moyen d’une griffe à foin télescopique montée sur rails, dont l’éleveur a équipé la cabine d’un système de pesée embarquée et d’une caméra thermique afin d’identifier les éventuelles formations de cheminées thermiques dans les cellules.
Les 800 m² de toiture du bâtiment sont munis d’une sous-toiture permettant, via un total de 5 m² d’ouverture d’aspiration, de préchauffer l’air prélevé de 30 à 40 %. Un bâtiment annexe accueille l’échangeur thermique (alimenté en eau chaude par la chaudière biomasse) et le ventilateur. Un système de volets réglables permet un recyclage de l’air présent dans le séchoir.
À une distance de sécurité du séchoir, la chaudière biomasse (220 kW) est logée dans un container adapté, jouxtant un silo à combustibles de 10 m³. Ce dernier est muni d’un couvercle à ouverture manuelle, permettant un remplissage via un chargeur télescopique au fur et à mesure des besoins, au départ du stock principal de plaquettes situé sous un hangar couvert.
L’ensemble et les paramètres de séchage de chaque cellule sont commandés via un panneau de contrôle central, conçu sur mesure pour l’installation. Selon les réglages indiqués et les informations fournies par diverses sondes, le séchoir commande automatiquement le démarrage de la chaudière lorsque le préchauffage en toiture ne suffit plus (temps nuageux, nuit).
Enfin, une partie des besoins en électricité sont fournis par des panneaux photovoltaïques installés sur le toit de l’étable.
L'autoproduction de plaquettes : l'objectif 2022
Lors de la campagne de séchage 2021, 110 MAP (m³ apparent de plaquettes) ont été autoproduits et consommés, complétées par 30 MAP achetés à un fournisseur de plaquettes. L’autoproduction des plaquettes au sein de l’exploitation est réalisée en faisant appel à un prestataire externe pour le broyage en un calibre adapté à la chaudière. Le séchage est réalisé sous hangar ventilé, ou via la cellule de séchage à plat dont est équipé le séchoir. Philippe Counasse prévoit d’être autosuffisant sur sa consommation de plaquettes dès la saison 2022.